Introduction: cloth-bound books and their audiences
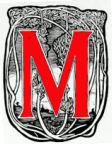
ost Victorian books and magazines were bound in a cloth casing. Though developed in the eighteen twenties, when they was first used in the publication of Keepsake Annuals, cloth and boards became increasingly popular and were ultimately the most characteristic form of the period. These trade bindings were the product of the Industrial Revolution: cheap to produce and rapid in manufacture, they were able to respond to the ever-expanding demands of a large and profitable market. Books bound in leather had serviced the cultural requirements of the aristocracy and social elite (who typically bought their books unbound, and had them bound to their own taste); books in cloth, on the other hand, were targeted at the purse of the business and professional middle-classes. Part of a commodity culture in which artefacts were made using industrial techniques, these books were participants in the process of democratization, making texts available to a class which had improving standards of literacy and wanted to participate in the wider world of ideas. The ‘middle rank’ also wanted to possess books as signs of their educational attainment, to express their wealth, and to build a cultural identity. Cheap publications or at least relatively inexpensive publications were in this sense the agents of social change and realignment, the focus and medium of what we might describe, in Pierre Bourdieu’s celebrated terms, as the consumers’ desire for ‘cultural capital.’

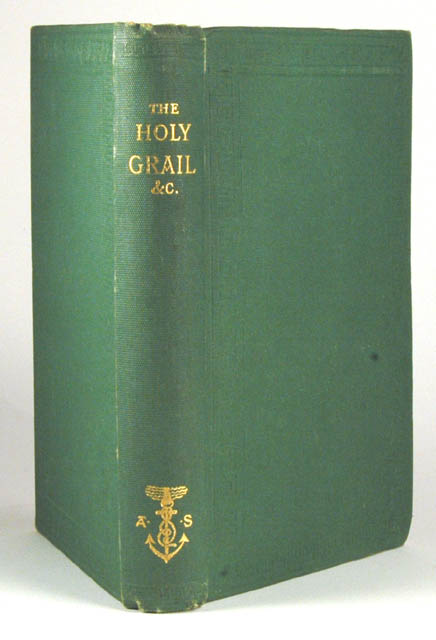
Left to right: (a) Idylls of the King. (b) The Holy Grail and Other Poems. [Click on these images for larger pictures.]
All classes of literature were dressed in cloth liveries, and retail prices were often very low. Charles Dickens’s novels were bound in cloth after they had appeared in the form of serialized parts, and cost between 5 shillings and 7/6, and the same is true of fictions by William Makepeace Thackeray. Robert Browning’s poems were inexpensively issued and Tennyson’s collections left the shelves at prices between two shillings and ten. Tennyson is indeed a prime example of this type of publishing. No matter how exotic, Tennyson’s texts were contained in cheap, plain bindings, an approach that contributed significantly to his popularity by reaching out to an audience with a limited income. Good examples of this economic functionality are Idylls of the King and The Holy Grail and Other Poems.
Other types of books were just as accessible to those with middle-class incomes of between a thousand and two thousand pounds per annum. The gilt covered gift books of the 1860s were typically priced between 10/6 and 36 shillings, although they represented extremely good value for a luxury item. John Leighton, William Harry Rogers, John Sliegh, Robert Dudley, and Albert Warren were the leading practitioners whose gilt designs embellished cloth-clad books, and many anonymous artists were employed in the same field. Parallel publications intended for the working classes were also widely available, made as cheaply as possible, and making use of the same, economical medium.
The marketing, retailing and dissemination of these works are the subject of wide-ranging scholarship and speculation. Less well-known is their physical production – how they were made, how publishers kept their cost down, and who produced them. Scholars such as Ruari Maclean (1963, 1972), Sybille Pantazzi (1961) and Edmund King (2003) have charted the material form of cloth bindings, but there is currently no detailed modern study that explores the practicalities of making. More surprising is the absence of Victorian monographs explaining how the books were made at the time of production, and the only information available to the modern researcher has to be taken from contemporary encyclopaedias, reference volumes and articles in magazines. The following section explains how the books were made by drawing on extracts from these sources.
Cloth casings: how the books were assembled and decorated
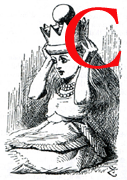
loth cased books were produced by a wide variety of binders, the most significant of which were located close to the heart of the publishing trade in the capital. Burn and Co., Leighton & Hodge, Remnants, and Virtue and Westley’s are perhaps the most celebrated. Their productions can be identified by the small binders’ tickets that are placed on the rear paste-down; Ball gives a detailed listing of the companies and locations (pp. 169–192), and King reproduces the tickets of the primary firms (pp. 267–270). Each binder has a style which overlaps with the style of the binding designer, although the technologies of production were shared by all.
The basic units were the cloth, which came in several grains (Ball, pp.129–142) and were dyed a variety of colours, and the boards, which were made of card. The spine or back-strip was made of canvas, or paper, which was often re-used from left-over newspapers. These elements were assembled using an industrial procedure. It is outlined in the 1854 edition of Charles Tomlinson’s Cyclopaedia of Useful Arts, which describes bookbinding in the premises of Remnant, Edmonds and Remnant (pp.152–162).
.The cases are then made up, with great rapidity, by two men, one of whom covers the inside with a layer of glue; then places two mill-boards in their proper position on the cover, so as to form the stiff sides, the space between the two depending, of course, on the thickness of the book. He then turns the cover over, and rubs the cloth firmly down with a cloth rubber … He then tosses the cover to [another] man, who places a strip of paper or canvass along the [space] between the two boards, and then folds down the projecting edges of the cloth over the boards, smoothing them down with the edge of a flat piece of stick with a blunt point at each end, and then drawing the point of the stick down the boundary lines between the back and the sides [p.159].
Having secured the boards to the cloth and to the strip that will become the spine, the next step involves the embossing and application of gilt decorations. This was done on an arming press which imprinted (or embossed) shapes into the surface of the cloth and was also used to impress the gilt design which was cut into a brass die. The Cyclopaedia gives a clear outline:
When the covers thus formed are perfectly dry, they are embossed and gilt. The ornaments which are simply produced by pressure are called blind-blocking, and when done by hand blind-tooling; while the gilt ornaments or lettering are called gold-blocking or gold-tooling. The machines employed in both descriptions or ornament are called blocking presses … The ornamental pattern for the back of the sides is cut out in a thick plate or block of brass, and is fixed in the upper bed of the press by means of a dove-tail joint. This upper bed is furnished with a cavity containing a gas-pipe with a row of jets for heating the die by conduction of heat from the upper bed. The cloth covers are inserted within metal rules, which serve as a gauge, by a man who sits before the press, while another man swings round with all his strength a long lever, whereby the upper bed is brought down a few inches upon the case in the lower bed, and embosses the impression. When the cases are completed in this way, they are taken to the gilders, who cover the parts intended to be gilt with a thin layer of ovalbumin or white of egg, called glaire, and then with a film of leaf-gold. The covers are then passed to a gold-blocking press containing a plate or block, in which are set up the lettering and other ornaments intended to be gilt. The letters may either be set up in movable type, or cut out of one solid piece of brass. For the ornaments, the latter course is adopted. The block is heated by jets of gas playing in a cavity of the upper bed, and the cover being carefully introduced into a gauged bed, the man moves a handle around, which brings the heated plated with a gentle and equable pressure down upon the cover, and permanently fixes the letters or device [p.159].
This extract explains the main procedures, and more detail is given in Chambers’s Encyclopaedia of 1872, which notes the difference between the handicraft of previous generations and the industrial techniques of the nineteenth century:
Formerly, the ornamental and other work on the outsides of books was executed in a tedious and expensive way by hand. Now, the operation, at least as regards cloth boards, is done by two or three impressions on an arming press; perhaps not taking more than half a minute being employed to execute what in the older time would have occupied a week. When it is deemed necessary, for the sake of attractiveness, to stamp a peculiar device on the covers of a book, of which thousands are required, the design is referred to an artist … his design is cut in brass or steel; and this, in the form of a metal block, gives the stamp at a blow by the arming-press. When the design is to be gilt, leaf-gold is previously applied. The block being heated, gives a firm and clear impression. Such is the expeditious method of titling and ornamenting with blank and gold tooling … [p.226].
This process was always efficient and cost-effective: a hundred covers could be completed in an hour and many more, using a combination of machinery and intense labour, over the following hours. As the Cyclopaedia (1854), explains, ‘In a large establishment, such as Messrs. Remnant’s, the whole impression of an octavo work, consisting of a thousand copies … can be done up’ (p. 159) in a couple of days. This was as workmanlike as the process could be, and the only complication was the retrieval and re-use of the gold, the single precious material. Once the cloth had been glued to the boards and back-strip, embossed and gilded, it was a matter of making sure there was no wastage:
As the covers are removed, they are taken by a boy, who wipes off the superfluous gold with a piece of thick rag, which thus gradually absorbs the fragile [gold] leaf, and in the course of two r three months this rag is so valuable that it is sold for perhaps 20 or 30s. to the gold refiner, who burns it in a covered crucible, and thus recovers the precious metal [p.159].
All that remained, finally, was to attach the casing to the text-block. This was a matter of sticking the whole together using glue. Although some cloth bindings were stitched (a technique used with more ‘serious’ literature), the cloth was usually glued onto the body of the book to create a ‘perfect binding’.
The covers thus formed are next adjusted to the books, which we left in the standing-press. The covers are secured to the books by glueing the canvas strips which project on each side of the book to the boards, and to conceal this arrangement as well as the uncovered parts of the boards, and also to give a neat finish to the book, some colour called lining paper is glued in. The books are lastly put into the standing press for a few hours, and may then be said to be finished (Cyclopaedia, p.159).
The glue was of course gutta percha, which is described in the Encylopaedia of 1872 as a ‘tenacious’ material (p.226). Unfortunately it was never entirely stable, with the result that many cloth-casings, particularly those used for gift-books, would ultimately fall apart. Bound in coloured material and held together by a rubber-solution, these publications were never intended to last. That so many books survive without repairs (or ‘re-backing’) is nevertheless a tribute to the materials and especially to the ‘refined division of labour’ (Cyclopaedia, p.159) that produced them.
Acknowledgement
I am deeply indebted to Mr Edmund King, the author of essays on John Leighton and W. H. Rogers, for help in the preparation of this entry.
Related Material
Works Cited and Sources of Information
Ball, Douglas. Victorian Publishers’ Bindings. London: The Library Association, 1985.
‘Book-Binding’ Penny Magazine. London: Knight, 1842, p.383.
Chambers’s Encyclopaedia. Philadelphia: Lippincote, 1872. 10 vols. Volume 2.
Jamieson, Eleanore. English Embossed Bindings 1825 –1850. Cambridge: Cambridge University Press, 1972.
King, Edmund. Victorian Decorated Trade Bindings, 1830–1880. London: The British Library & Newcastle: The Oak Knoll Press, 2003.
Maclean, Ruari. Victorian Book Design and Colour Printing. London: Faber & Faber, 1963.
Maclean, Ruari. Victorian Publishers’ Book-Bindings. London: Gordon Fraser, 1974.
Pantazzi, Sybille. ‘Four Designers of English Publishers' Bindings, 1850-1880’. Papers of the Bibliographical Society of America55 (1961): 88-99.
Tomlinson, Charles.
Cyclopaedia of Useful Arts. London: Virtue, 1854.
Last modified 14 December 2013